A felületkezelés megválasztása olyan probléma, amellyel minden tervező szembesül.Sokféle felületkezelési lehetőség áll rendelkezésre, és egy magas szintű tervezőnek nemcsak a tervezés gazdaságosságát és praktikusságát kell figyelembe vennie, hanem az összeszerelési folyamatra, sőt a környezetvédelmi követelményekre is figyelnie kell.Az alábbiakban röviden bemutatunk néhány általánosan használt kötőelem-bevonatot a fenti elvek alapján, a kötőelemekkel foglalkozó szakemberek számára.
1. Elektrogalvanizálás
A cink a kereskedelmi kötőelemek leggyakrabban használt bevonata.Az ára viszonylag olcsó, és a megjelenés is jó.A gyakori színek közé tartozik a fekete és a katonai zöld.Korróziógátló teljesítménye azonban átlagos, korróziógátló teljesítménye a legalacsonyabb a horganyzási (bevonat) rétegek között.Általában a horganyzott acél semleges sópermet tesztjét 72 órán belül elvégzik, és speciális tömítőanyagokat is használnak annak biztosítására, hogy a semleges sópermetezési teszt 200 óránál tovább tartson.Az ára azonban drága, ami 5-8-szorosa a hagyományos horganyzott acélénak.
Az elektrogalvanizálási folyamat hajlamos a hidrogén ridegségére, ezért a 10.9-es fokozat feletti csavarokat általában nem kezelik galvanizálással.Bár a hidrogén kemencével bevonatolás után eltávolítható, a passziváló fólia 60 ℃ feletti hőmérsékleten megsérül, ezért a hidrogén eltávolítását galvanizálás után és passziválás előtt kell elvégezni.Ennek rossz a működése és magas a feldolgozási költsége.A valóságban az általános gyártóüzemek nem távolítják el aktívan a hidrogént, kivéve, ha konkrét vásárlók kérik.
A horganyzott kötőelemek nyomatéka és előfeszítő ereje közötti összhang gyenge és instabil, és általában nem használják fontos alkatrészek összekapcsolására.A forgatónyomaték-előfeszítés konzisztenciájának javítása érdekében a kenőanyagok bevonása utáni bevonat módszere is használható a nyomaték előfeszítés konzisztenciájának javítására és fokozására.
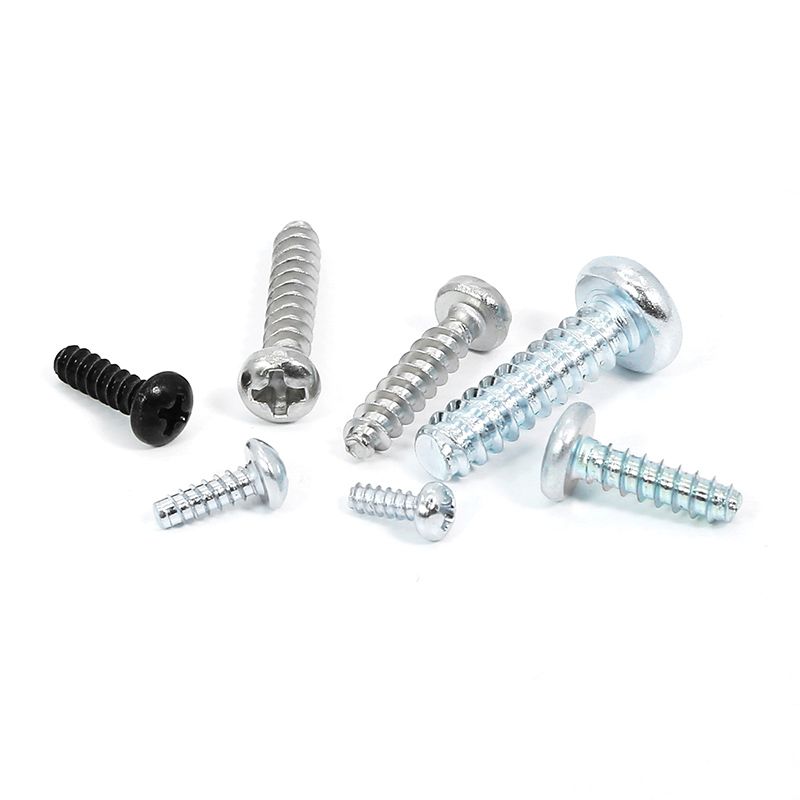
2. Foszfátozás
Alapelv, hogy a foszfátozás viszonylag olcsóbb, mint a horganyzás, de a korrózióállósága rosszabb, mint a horganyzásé.Foszfátozás után olajat kell felvinni, és annak korrózióállósága szorosan összefügg a felvitt olaj teljesítményével.Például foszfátozás után, általános rozsdamentesítő olajjal és semleges sópermetezéssel csak 10-20 órán keresztül.A kiváló minőségű rozsdagátló olaj alkalmazása akár 72-96 órát is igénybe vehet.De az ára 2-3-szorosa az általános foszfátozó olajénak.
A kötőelemekhez két általánosan használt foszfátozási típus létezik, a cink alapú foszfátozás és a mangán alapú foszfátozás.A cink alapú foszfátozás jobb kenési teljesítményt nyújt, mint a mangán alapú foszfátozás, és a mangán alapú foszfátozás jobb korrózióállósággal és kopásállósággal rendelkezik, mint a horganyzás.225 és 400 Fahrenheit (107-204 ℃) közötti hőmérsékleten használható.Főleg néhány fontos komponens csatlakoztatásához.Mint például a motor hajtórúdcsavarjai és anyái, hengerfej, főcsapágy, lendkerékcsavarok, kerékcsavarok és anyák stb.
A nagy szilárdságú csavarok foszfátozást használnak, ami szintén elkerülheti a hidrogén ridegségével kapcsolatos problémákat.Ezért az ipari területen a 10.9-nél magasabb osztályú csavarok általában foszfátozó felületkezelést alkalmaznak.
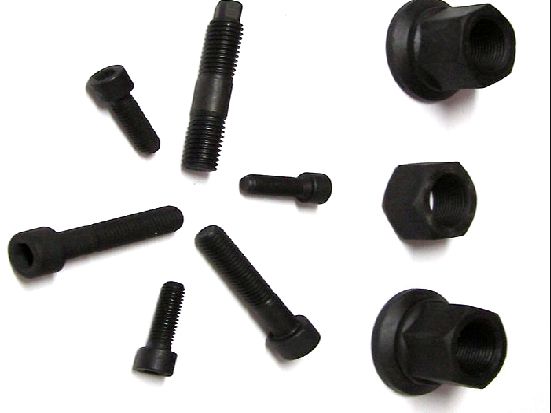
3. Oxidáció (feketedés)
A Blackening+Oiling egy népszerű bevonat az ipari rögzítőkhöz, mert ez a legolcsóbb és jól néz ki üzemanyag-fogyasztás előtt.Feketedéséből adódóan szinte nincs rozsdagátló képessége, így olaj nélkül is gyorsan berozsdásodik.A sóspray-teszt olaj jelenlétében is csak 3-5 óráig tarthat.
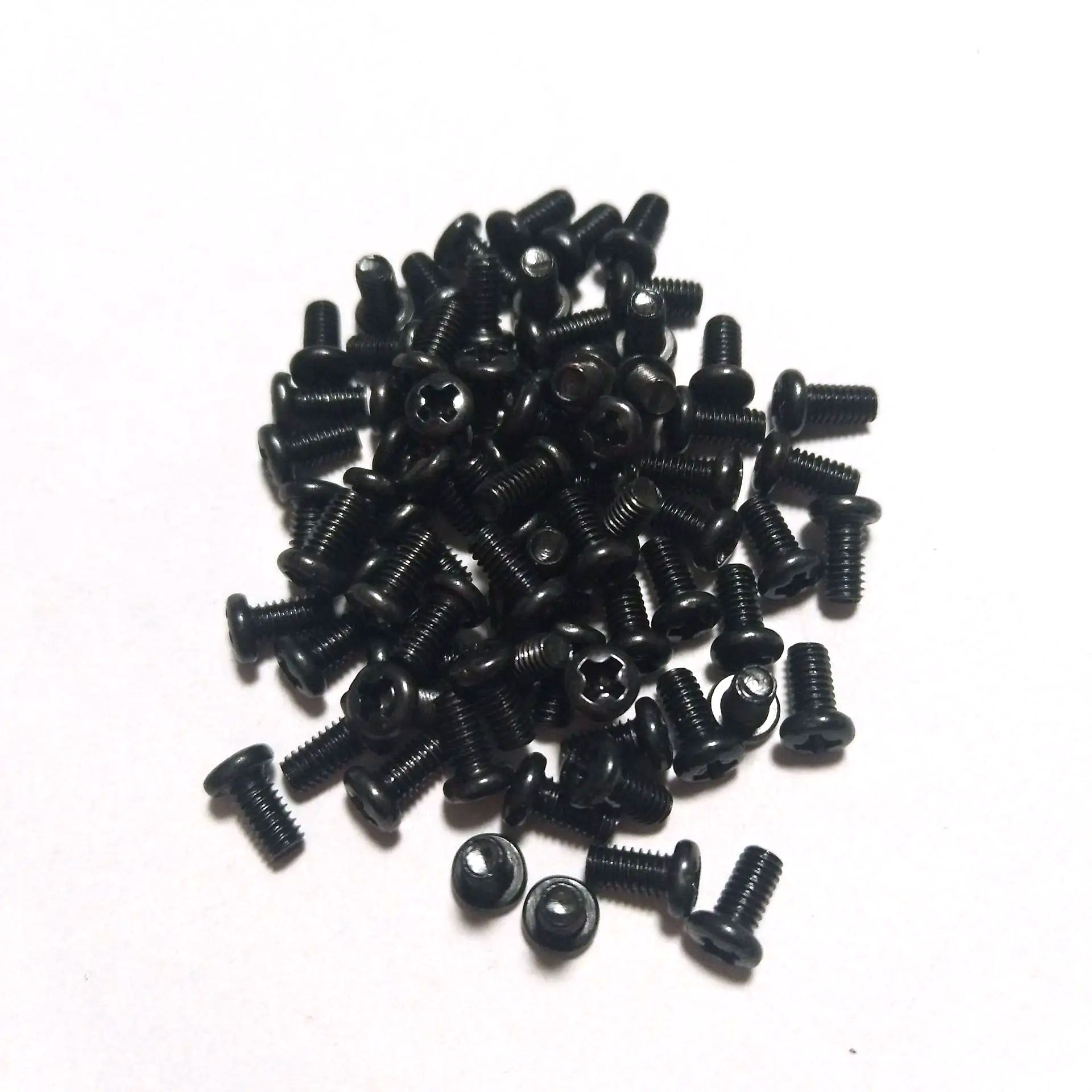
4. Galvanizálási válaszfal
A kadmium bevonat kiváló korrózióállósággal rendelkezik, különösen tengeri légköri környezetben, összehasonlítva más felületkezelésekkel.A kadmium galvanizálásának folyamatában a hulladékfolyadék kezelési költsége magas, és ára körülbelül 15-20-szorosa a galvanizálási cinkének.Tehát nem általános iparágakban használják, csak meghatározott környezetekben.Olajfúró platformokhoz és HNA repülőgépekhez használt rögzítőelemek.
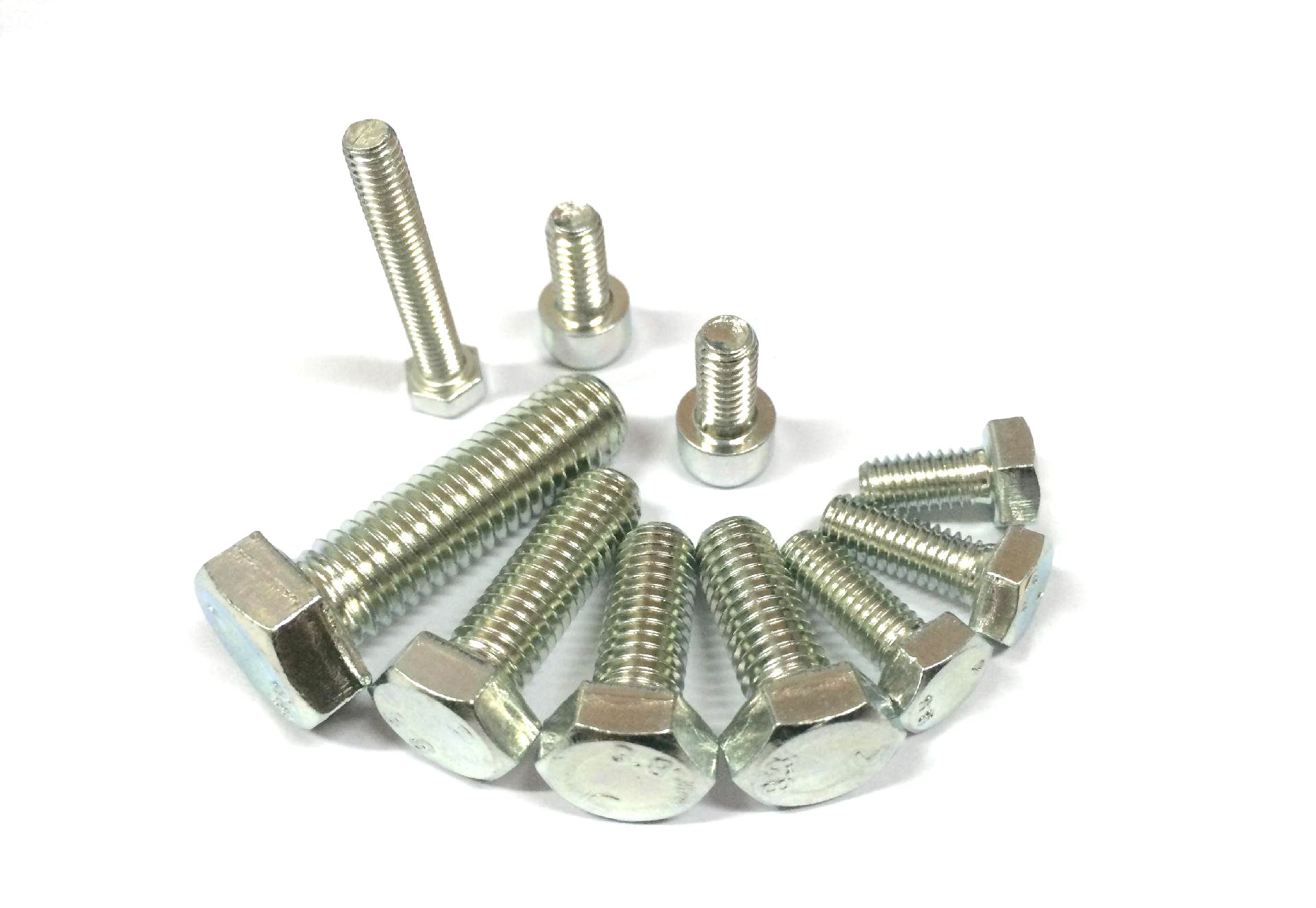
5. Krómozás
A krómbevonat nagyon stabil a légkörben, nem könnyű megváltoztatni a színét és elveszíteni a fényét, nagy keménységgel és jó kopásállósággal rendelkezik.A kötőelemeken a krómozást általában dekorációs célokra használják.Ritkán használják magas korrózióállósági követelményekkel rendelkező ipari területeken, mivel a jó krómozott kötőelemek ugyanolyan drágák, mint a rozsdamentes acél.Csak akkor, ha a rozsdamentes acél szilárdsága nem kielégítő, krómozott rögzítőelemeket használnak helyette.
A korrózió megelőzése érdekében a krómozás előtt először rezet és nikkelt kell bevonni.A krómbevonat 1200 Fahrenheit-fok (650 ℃) magas hőmérsékletnek is ellenáll.De van egy probléma a hidrogén ridegségével is, hasonlóan az elektrogalvanizáláshoz.
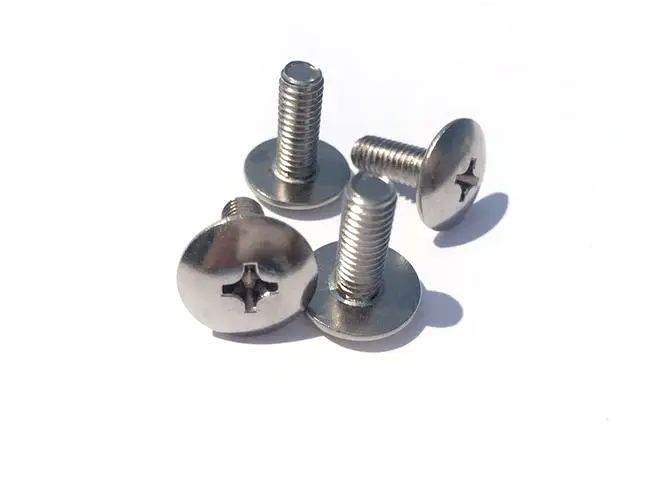
6. Nikkelezés
Főleg olyan területeken használják, ahol korrózióvédelemre és jó vezetőképességre van szükség.Például a járműakkumulátorok kimenő kapcsai.
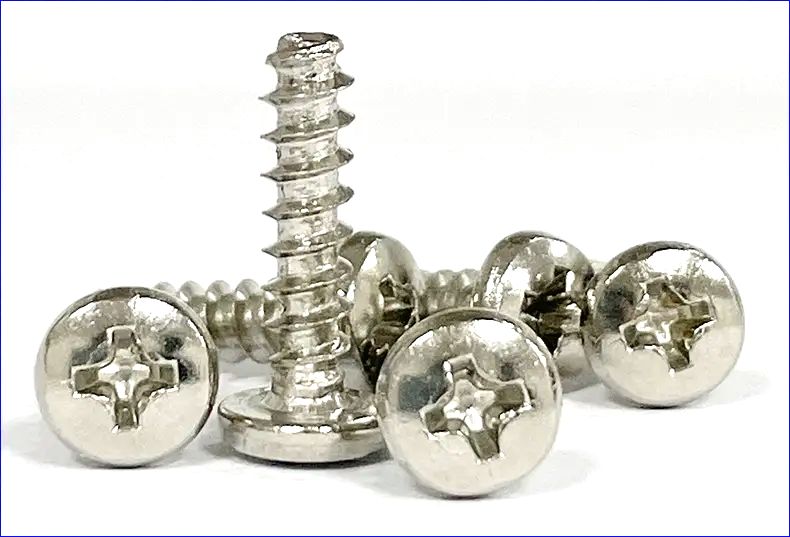
7. Tűzihorganyzás
A tűzihorganyzás egy hődiffúziós bevonat, amely folyadékká hevített cinket tartalmaz.A bevonat vastagsága 15 és 100 μm között van.És nem könnyű irányítani, de jó a korrózióállósága, és gyakran használják a mérnöki munkákban.A tűzihorganyzás során súlyos szennyeződések lépnek fel, beleértve a cinkhulladékot és a cinkgőzt.
A vastag bevonat miatt nehézségeket okozott a kötőelemek belső és külső meneteinek becsavarása.A tűzihorganyzás feldolgozási hőmérséklete miatt nem használható 10.9 (340-500 ℃) feletti kötőelemekhez.
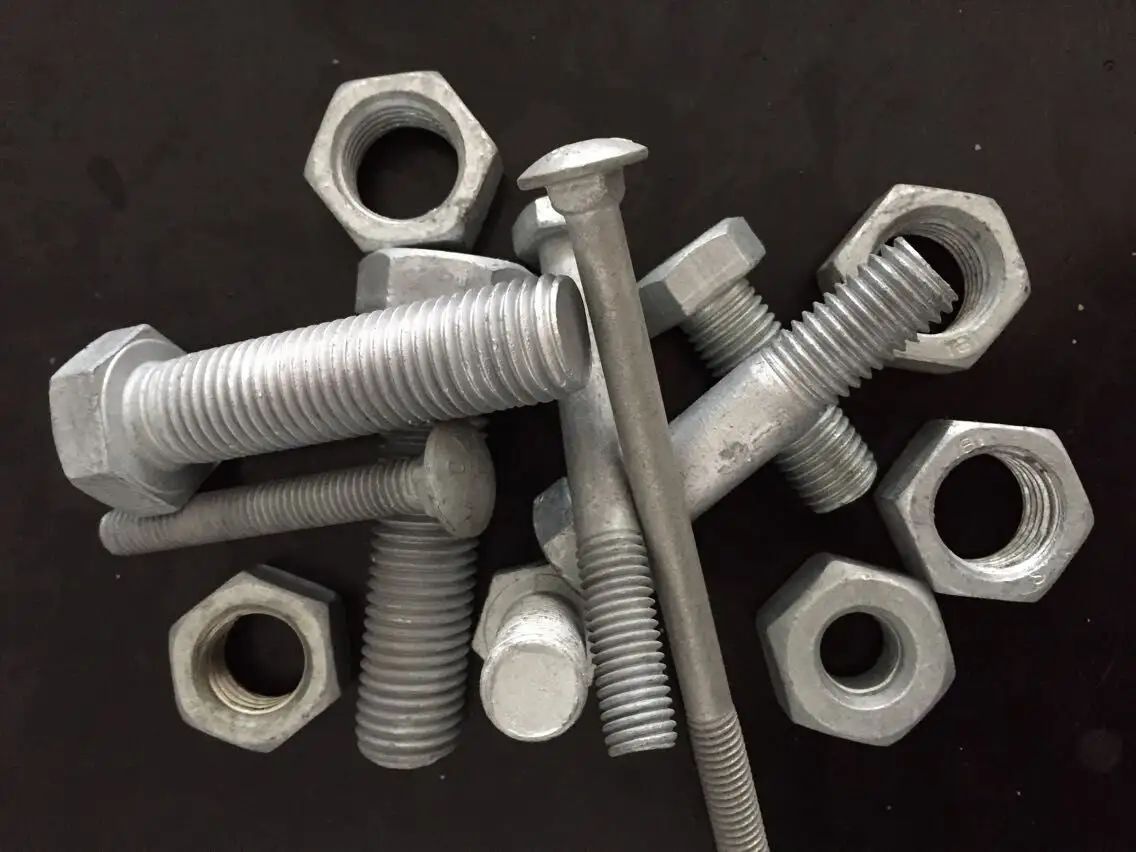
8. Cink beszivárgás
A cink-infiltráció egy cinkpor szilárd kohászati termikus diffúziós bevonata.Egyöntetűsége jó, menetekben és zsákfuratokban is egyenletes réteg érhető el.A bevonat vastagsága 10-110 μm.A hiba pedig 10%-ig kontrollálható.Tapadási szilárdsága és korróziógátló teljesítménye az aljzattal a legjobb a cinkbevonatoknál (például elektrogalvanizálás, tűzihorganyzás és Dacromet).Feldolgozási folyamata szennyezésmentes és a leginkább környezetbarát.
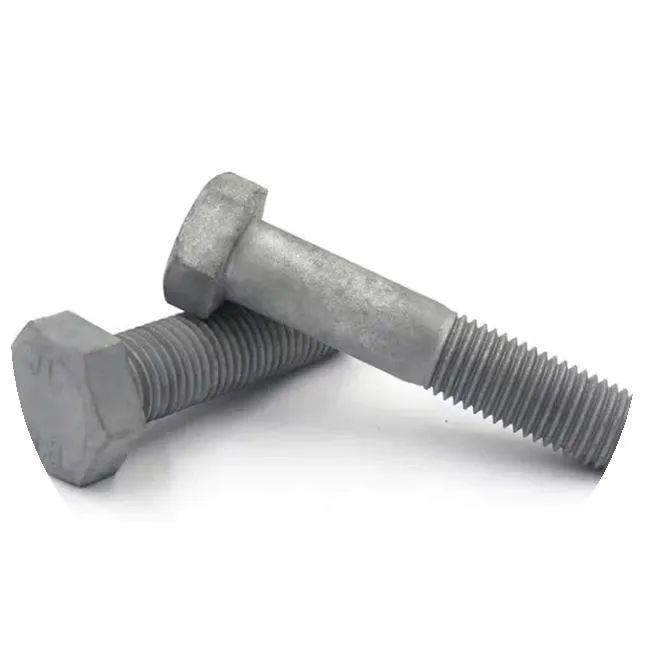
9. Dacromet
Nincs probléma a hidrogén ridegségével, és a nyomaték előfeszítési konzisztenciája nagyon jó.A króm és a környezetvédelmi kérdések figyelmen kívül hagyása nélkül a Dacromet a legmegfelelőbb a nagy szilárdságú kötőelemekhez, amelyek magas korrózióvédelmi követelményekkel rendelkeznek.
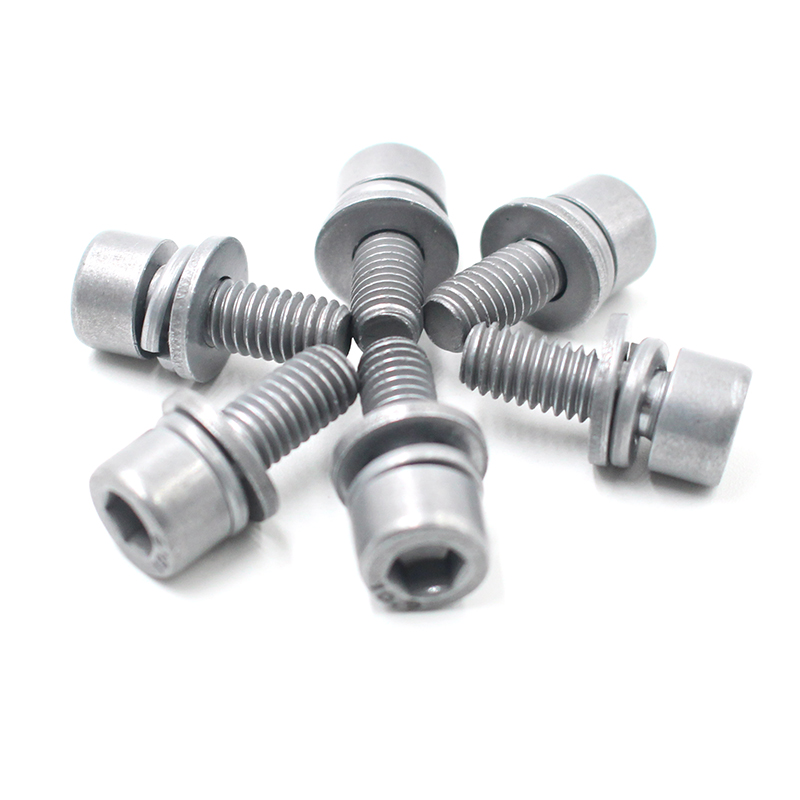
Feladás időpontja: 2023. május 19